Potting is an essential process in the manufacturing of LED power supplies, as it protects electronic components from environmental factors, enhances thermal management, and provides mechanical support. The three most commonly used potting materials are silicone, resin, and polyurethane. Each material has its unique properties, advantages, and disadvantages. In this blog, we will compare these materials to help you understand their differences and applications.
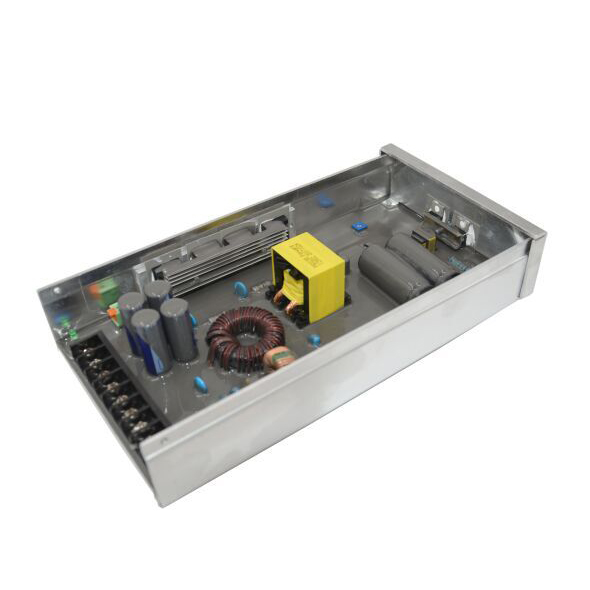
1. Silicone
Advantages:
- Temperature Resistance: Silicone is renowned for its ability to withstand extreme temperatures, typically ranging from -50°C to 200°C, making it suitable for high-temperature environments.
- Flexibility: It maintains its flexibility over a wide temperature range, which helps in absorbing mechanical stresses and vibrations without cracking.
- Electrical Insulation: Silicone offers excellent electrical insulation properties, crucial for preventing short circuits in high-voltage applications.
- Chemical Resistance: It is resistant to water, ozone, and a variety of chemicals, which enhances its durability in harsh conditions.
Disadvantages:
- Cost: Silicone is generally more expensive than other potting materials.
- Adhesion: It may have lower adhesion to certain substrates compared to resin and polyurethane, which can limit its applications.
2. Resin
Advantages:
- Adhesion: Resin provides strong adhesion to a wide range of surfaces, offering excellent mechanical support and protection.
- Durability: It is durable and provides robust protection against moisture, dust, and other environmental factors.
- Chemical Resistance: Resin is resistant to many chemicals, making it suitable for use in industrial environments.
Disadvantages:
- Brittleness: Resin can become brittle over time, particularly in cold temperatures, which may lead to cracking.
- Limited Flexibility: It is generally less flexible than silicone and polyurethane, making it less suitable for applications subject to significant vibrations or thermal cycling.
- Temperature Range: Resin typically has a narrower temperature range than silicone, which can limit its use in extreme conditions.
3. Polyurethane
Advantages:
- Flexibility and Toughness: Polyurethane offers a good balance of flexibility and toughness, making it ideal for applications that experience vibration and mechanical stress.
- Chemical Resistance: It is resistant to moisture, chemicals, and abrasion, providing reliable protection in harsh environments.
- Cost-Effective: Polyurethane is often more cost-effective than silicone, offering an economical option for many applications.
Disadvantages:
- UV Stability: Polyurethane can degrade when exposed to UV light over time, leading to discoloration and reduced performance.
- Temperature Range: It has a more limited temperature range compared to silicone, which can restrict its use in extreme temperature conditions.
- Moisture Sensitivity: Some polyurethane formulations can be sensitive to moisture during curing, requiring careful control of the potting environment.
Conclusion
The choice of potting material for LED power supplies depends on the specific requirements of the application. Silicone is ideal for high-temperature environments and applications requiring flexibility, while resin offers strong adhesion and durability. Polyurethane provides a cost-effective solution with good flexibility and chemical resistance. Understanding the advantages and disadvantages of each material will help ensure the reliability and longevity of your LED power supply.
When selecting a potting material, consider factors such as operating temperature, environmental conditions, mechanical stress, and cost to ensure optimal performance and protection for your LED power supplies.
Leave a Reply